What is Depo-X?
It is a dynamic system that is designed to effectively manage the operations you perform in your warehouse and carries out warehouse stock status and movements in real time. Its purpose is to ensure the error-free completion of the operation without paper, in the shortest time, with the least human and machine resources, to make decisions, to monitor the operations performed live and to present the information of the operations performed to the user in reports.
"Depo- X" is an application that has proven itself with its easy-to-use, user-friendly interfaces, fast and efficient structure, and its success in complex storage applications in the Automotive, Retail, Stationery, Electronics, Beverage, Telecommunication sectors and in the needs of Logistics Service Providers.
Today, warehouse management does not stay within the boundaries of the physical warehouse. Warehouse Management is becoming more and more difficult to manage with the developing and growing service areas day by day. Inventory management, inventory planning, cost management, IT applications and communication technologies to be used are all related to warehouse management. Today, container storage, loading and unloading are now covered by warehouse management. Even production management is highly interconnected with warehouse management. "Depo- X" offers maximum control authority in all these processes in your warehouse. "Depo- X" will be your biggest business partner in your warehouse, offering solutions ahead of the day in developing warehouse management techniques.
Why Depo-X ?
"Depo- X" allows you to monitor the physical status of your warehouse statistically and visually from anywhere at any time. Thanks to the '3D-MC (3D Visual - Management Console)' interface developed by Lobitek, it allows you to access and make changes to the address, quantity, dimensions and many similar information about the pallets on the shelves as if you were in the physical warehouse. '3D-MC' has made a big difference among warehouse management systems with its ease of use, fluent screens and functionality.
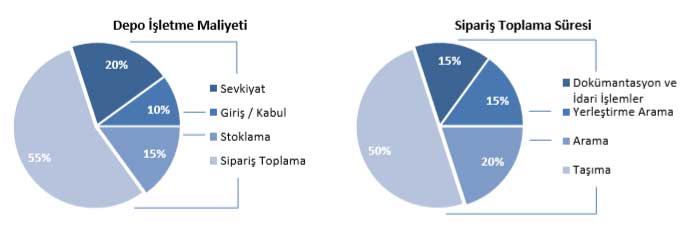
'Order Picking' operations consume a large part of Warehouse Operating Costs. "Depo- X" minimizes the loss of workforce, i.e. the cost, by organizing the pickers in an optimum way through hand terminals in 'Order Picking'. Optimizing the picker routes according to the work orders, "Depo- X" allows the pickers to finish their work as soon as possible.
Depo-X Innovations
"Depo- X - IDS(Integration Data Service)" Thanks to its structure, it can easily work integrated with all ERP programs. IDS is an integration interface developed by Lobitek that works over WebService. It is the basic structure that provides data transfer and control from a central point to all locations in multi-point structures. Thanks to this structure, the integration work between the ERP system and Depo- X IDS is done once, and when new locations are created, the data is automatically distributed to the locations through the same system.
Depo- X architecture is designed as ID-based and in case of the need to update master information over time; relevant updates can be made without any current or historical data loss. (for example, if the desired product code "X" is changed to "Y" at time "t"; there is no current or retrospective loss in stocks, existing work orders, in-store stock movements and order records).
Thanks to Depo- X product management, the assembly processes of your configured products can be tracked as Container (Container), Parent Product, Child Product and Serial Numbers.
Again, a strict control mechanism is established for catalog products (pallets with C...) whose versions are created within a certain discipline, and when necessary, a part of the content, such as an electronic card, is removed from the pallet and the pallet is used as a mixed pallet (Catalog and Version information is hidden). With the completion of missing configurations, the product is withdrawn to the relevant version (catalog conversion), preventing the formation of idle stock. It is also possible to switch between product versions with the assembly process. Thus, a catalog product can be downgraded to a lower version by removing some product(s) or upgraded to a higher version by adding some products.
Depo-X Overview
It is a warehouse tracking and management system that manages the tracking and control of all storage processes of one or more warehouses within the company with person, time, address information.
Under "Depo-X";
- FIFO (FEFO,LIFO)
- Traceability
- Accuracy in Loading and Inventory
- Increase in Upload Speed
- Observability
- Reducing Paper Labor
- Management and Monitoring of Value Added Operations
- Direct connection to existing systems with On-Line and flexible ERP integration
- Fast and accurate counting with the help of advanced counting algorithms
- Warehouse space savings
- Fast efficient and labor-saving with In/Out, placement and order picking
Provided.
"Depo- X" software enables the warehouse entry, locating and placement of all kinds of products coming from outside as affected, monitoring the status of the products in the warehouse, making changes in the warehouse when desired, finding and controlling the shipment process by finding the pallets according to the prepared shipment orders.
The physical stock in the warehouse and all movements created in the system by "Depo- X" are recorded in the database and monitoring and evaluation reports on the transactions can be received instantly.
"Depo- X" (Warehouse Management System) consists of 3 main modules as Server, Client and RF applications. 'Windows 2003-2008 Server' operating system and 'SQL Server 2005-2008' database management systems must be installed on the server.
One of the 'MS Windows (XP, Vista, Windows 7, Windows 8)' applications must be installed on the client computers and 'Microsoft Terminal Service' must be installed on the server for hand terminal applications.
Depo- X Scope
"Depo- X" Warehouse Management System consists of the following main processes.
- Warehouse Receiving / Acceptance Operations
- Placement Procedures
- Storage Operations
- Shipment Operations
- Counting Operations
- Value-Added Transactions
- Reporting Operations
Depo-X Warehouse Receiving / Acceptance Operations
- Orderly procurement of material
- Checking that the quantity and quality are at the desired level
- Sending the material to the warehouse or to the places where it is needed
All products entering the system on pallets must be labeled with appropriate label types indicating the pallet usage class.
- A……..1 (A → Single product pallet)
- M…….2 (M → Mixed palette)
- C………3 (C → Catalog Pallet)
The barcodes on the labels must be capable of being read remotely by existing terminals. For products without labels, labeling is done in a controlled manner at the warehouse entry point.
Bulk products that will be placed directly at the storage addresses without pallets have labels containing product and production information.
Entry to the warehouse through purchase orders or returns from customers are within the scope of entry. If the products coming to the warehouse come from the production facilities, the existing barcode label will be scanned or if they come through purchase, a new label will be created. Inventory movements are also created for all kinds of entry, exit, transportation, transfer and counting operations in the warehouse.
In this way, the transaction performed in the warehouse, the personnel performing it, the location and the transaction time are tracked in detail.
Entry / Acceptance Transactions;
Order Dependent Palletized Entry
- Order Dependent Palletless Entry
- Crawler Free Entry
- Trackless Free Entry
- Fast Pallet Entry (Based on Order)
- Input Value Added Operations (Label Reading, Assembly, etc...)
Depo-X Placement Operations
- Determining the address to be stored and recording the relevant work orders
- Transportation
- Placement
After the labeling process of the pallets arriving at the warehouse, the placement process will be carried out. With warehouse parameters, warehouse goods acceptance processes can be designed in different ways on the basis of Ordered, Manual, Zone and Strategy management. During placement, depending on the type of operation, the operator will read the Work Order, Pallet Barcode and the address to be placed. Thus, the physical address of each pallet in the warehouse can be monitored instantly..
Products can be relocated by making arrangements in the warehouse. In this case, the operator takes the product to be relocated, reads the product code and the address where it was received. When he puts the product in the new location, he reads the new address this time. Thus, the location of the product is updated.
Placement Operations;
- Emirli Forklift Operations
- Elective Forklift Operations (Ordered)
- Address to Address Pallet Transfer
- Pallet Split from Pallet
- Pallet Assembly
- Manual Pallet Placement
- Mixed Pallet Operations
- Pallet Transfer Between Warehouses (Free)
- Pallet Transfer Between Warehouses (Ordered)
- Parcel Transfer Process
- Pallet Transfer from Shipping Address to Picking Address
- Product and Address Handling in the Picking Compartment
Shipment Operations;
- Free Shipment
- Automatic (Ordered) Shipment Picking
- Collecting Shipments by Product Shipment Group (PSG) (2.5Lt Pet, Tetra Carton, etc...)
- Creating Shipment Parcels
- Loading Shipment Parcels
- Parcel Control
- Vehicle Loading
- Vehicle Final Check
Depo-X Storage Operations
Warehouse Management System to address existing products within the warehouse;
- Outdoor Pallet Addresses
- Rack Pallet Addresses
- Outdoor Bulk Product Addresses
- Rack Palletless Product Addresses
- Mixed Pallet Areas (Used in cases where the picking eye is insufficient; its use is similar to the picking eye)
- Stocking Fields with Parametric Properties
- Operations and Value Added Transactions Addresses
- Entry and Shipment Addresses
Can be created. Warehouse, Area and Address based parameters can be used for addressing and stocking in the warehouse.
Depo-X Shipment Operations
Products in the warehouse can be shipped for sales purposes in line with shipment work orders. Shipment work orders are prepared in the server system and transferred to "Depo- X Client" and "Depo- X Hand terminal" systems and wait for shipment.
Thanks to the "Depo- X" shipment tracking system, all orders, movements, pallets, rolls, parcels and transaction status related to the shipment can be monitored instantly on a single screen.
In line with the orders prepared in the main system, picking lists are created and picking orders are sent to pickers based on these lists.
- Picking, Sorting and Vehicle Loading in Intensive Warehouse Applications
- For Simpler Warehouse Operations, Vehicle Loading Options are Also Available Based on a Direct Work Order.
Depo-X Counting Operations
Stock status in the warehouse is continuously reported on product, version, lot and layout basis. In addition, the stock in the warehouse can be counted in desired periods. Counting can be done according to the following principles.
These; The counting of goods labeled with barcode is done quickly and healthily without interrupting the warehouse operation. Finished goods warehouse counting can be done at any time other than the year-end inventory count. All eyes in the entire warehouse or in a designated part are scanned and the pallet or product information is read and checked with the current situation. Address differences are corrected instantly and a counting effect movement is created by entering the quantity difference.
Counting Operations;
- Pallet Instantaneous Counting
- Periodic Counting
- Bulk Address Instant Counting
Depo-X Reporting Operations
Warehouse Management System software includes all kinds of detailed and summary reports for users and managers. Some of these are as follows;
- Warehouse Layout
- Performance Reports
- Available Product Report by Address
- Finished Goods Movement Reports
- Warehouse Stock Status Reports
- Warehouse Count Reports
- Referral Monitoring Reports
Depo-X Hand terminal(RF)
"Depo- X" helps you to perform your goods receiving operations effortlessly via the handheld terminal (RF). Main menus available on your handheld terminal;
- Acceptance Procedures
- Transfer Operations
- Exit Operations
- Shipment Operations
- Stock Conversions
- Administrator Operations
- Inquiry Procedures
You can perform many operations in their main headings
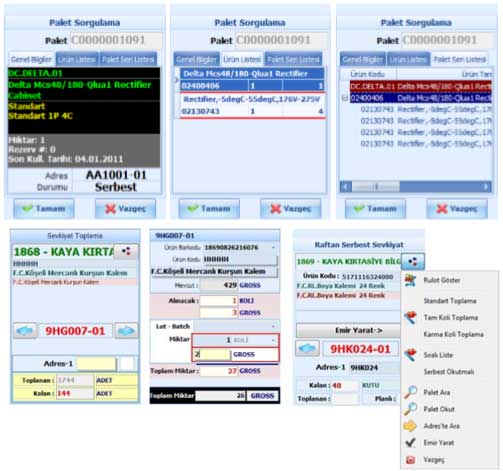
Depo-X Pallet Label
Pallet labels are barcoded labels that are attached / pasted on pallets, containers, boxes, barrels, etc. objects for transportation and storage purposes where materials are stored in bulk. The barcoded reference code on the prepared label is associated with the material code, lot, quantity, unit, status and address etc. information related to in-warehouse operations.
Depo-X Lot Tracking
Thanks to Lot Tracking, lot-based transactions can be made in all operations in the warehouse.
Depo- X Version Tracking
Products with different configurations or different software belonging to the same product code in the warehouse can be easily distinguished by the system thanks to version tracking and conversion, combination and separation between versions can be made.
'XTR1200A' Refrigerator
'V101' - 12 Program Version with White Door
'V102' - 14 Program Version with Red Door
'XTR1200A' in the form of V101, V102 versions.
Depo- X Asset Identification System
Serial No. It records and monitors the materials containing materials in accordance with the purpose of recall and maintenance of warranty information. Products can be tracked by serial number on unit basis if desired;
Container → parent product → child product can also be tracked with assembly information.
Depo- X Zone
It is the structure that enables the addresses in the warehouse to be grouped logically. Repository placement is done by sorting within strategies.
Depo- X Cross Dock
By ensuring that the material entered is directed to the shipment immediately or delayed without being placed in the warehouse, minimum use of warehouse resources is ensured..
Depo- X Placement in Computer Management
The most ideal placement address in the warehouse is assigned by taking into account the parameters based on Warehouse, Product Groups, Product and Address; if a place cannot be found, it is recorded in the task queue and notifications are made that the personnel in charge can follow.
Depo- X FIFO Application
It parametrically includes FIFO / FEFO / LIFO implementation algorithms for an efficient stock rotation.
Depo- X – CM
Depo- X / CM is a warehouse management and tracking system designed by Lobitek to manage all phases of the operation based on the Automotive Sector CKD operation.
In addition to all standard warehouse management processes, a comprehensive and unique warehouse management system that includes input frequency control, lot-based picking, packaging and shipment modules specific to the CKD operation has been created with the software.
Depo- X / CM – Basic Structure
- Depo- X / CM (Warehouse Management System) consists of 3 main modules: Server, Client and Handheld Terminal (RF) applications.
- Windows 2003-2008 Server operating system on the server and any of the SQL Server 2005-2008 database management systems as database.
- MS Windows (XP, Vista, Windows 7) applications must be installed on client computers.
- For handheld terminals, it is preferred to have Windows Mobile or WinCE Operating System.
Depo- X / CM - Data Distribution Model
- System data integrations are controlled and directed by the Distribution Service (DS) layer.
- In this way, multiple locations or databases can be accessed from a single point and all data traffic can be monitored from a single point.
- These services are used by Depo- X Connect application or ERP systems to display instant operation data.
- It is the integration layer where basic definition information (product, company...), movement data (delivery note, order...) and feedback (operation results) are made.
- In cases where web service integration is not possible, file-based integration is performed. In such cases, data is taken from files in txt, xml, excel formats with project-specific constructions and transferred to the Data layer under Integration Services. We can show the integration with WMF as an example.
Depo-X / CM – Vaulting
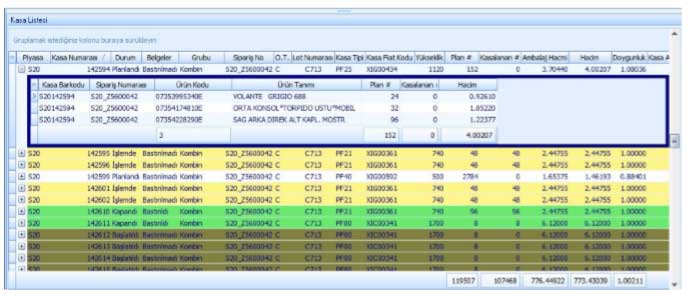
-
In case planning, the system aims to complete the case saturation to 100% and this information is listed on the screens together with the case volume and weight.
-
There are two types of stock in the warehouse;
-
Pallet and address stock
-
Cash register stocks (Free cash registers placed at cash register addresses or waiting to be loaded based on an order)
-
Regardless of whether the planned crates are 'ESR', 'IC', 'CKD' operations, the crates that are abandoned from shipment can also be stored as crate stock in the warehouse without deterioration with the alternative of returning to stock.
Depo- X / CM – Free Cash Register Creation and Linking
- In cases where the entire contents of the case packed for an order need to be canceled for some reason, the case is assigned as "free case" with the help of a hand terminal without canceling the case number. When this operation is done, the related order is returned to the balance as much as the contents of the case and the material stock remains in the case. Later, when the cash register is to be assigned to a different order, the cash register is connected to the desired order with the hand terminal application. The balance of the related order is deducted as much as the amounts in the cash register.
- With this application, the safe is broken and assigned to a different order without changing the safe number. Since it does not require the process of returning from the safe to the pallet, it provides retrospective tracking convenience. In addition, the cash registers waiting as free can be monitored from the cash register tracking screens.
- When we evaluate the application in an operative sense, since the case number does not need to change, the case can be broken down again in the appropriate areas in the field and kept on the shelves without the need for addressing.
- This is an application that applies to the whole market. The application is tried and actively used
- With lot transfer, stock and account balance between operations can be effortlessly transferred to a different operation. The transferred lot is deducted from the account balance and stock of the operation and transferred with the same barcode number without extra operations.
- When the handheld terminal (RF) user is picking for the CKD operation, the materials with picking priority based on the order will be reflected on the user screen. The operation will continue or stop with the user's approval.
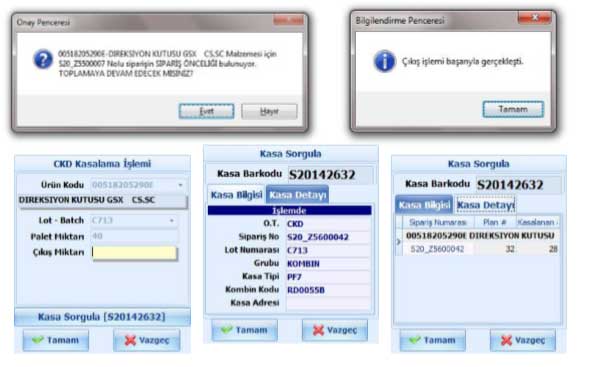
- The user guided during collection will collect the parts completely and accurately, saving time and cost.
Depo- X / CM – Virtual Container Creation
- This is a valid application for lot based orders.
- With this application, the in-case plan is prepared in the system, but unpacked cases, half cases waiting for processing and closed cases ready for shipment are all covered.
In this application, the time is opened as in the standard procedure for the container and lot for which a virtual transaction is desired. Then, on the virtual container creation screen, the previously shipped lot and container are selected. The crates to be loaded into the selected container are selected from the list and added. When the crate container mapping is completed, file creation is done and the system creates a shipment file in accordance with the WMF format. This file is executed in WMF and validation is done.
- With this work, virtual transactions can be made within the planned cases and within the cases that are in process, so virtual transactions can be made without disrupting and disrupting the currently functioning system. All steps of the packaging process can be carried out completely even though virtual processing has been performed. In this way, there is no need to follow the virtual container information and case contents from the lists and the risks of the virtual process are minimized. The application has been tested and actively used.
Depo-X / CM – Undo Transaction
- The transactions made in all processes of the operation can be undone through the system without losing the records. These processes are explained below.
- Input Waybill information correction; When there is a discrepancy between the e-waybill and the receipt document in the waybill entries that have been entered into the system but have not yet been entered and approved, changes can be made to the waybill information on the system, and the changes made are also reported back with integration. - Order registration
- Delete, Add or Correction; When it is necessary to make changes to lot or ESR orders that are automatically entered into the system, a change record can be created through WMF and the necessary changes can be made through the system even if the order has been started.
- Taking Back the Stocks of the Material Read into the Cash Register; The system allows to take back the stocks of the material read into the cash register for any reason from the cash register. With this process, it is possible to purchase part of the material from the cash register. By taking back the stocks, the order of the material in the cash register returns to the balance.
- Withdrawal of the cash register that has been read into the container; The system allows the stocks of the cash register that has been read into the container to be withdrawn for any reason. In this way, the case loaded in the container can be withdrawn if desired.
Depo- X / CM – Aircraft and Emergency Supply Tracking
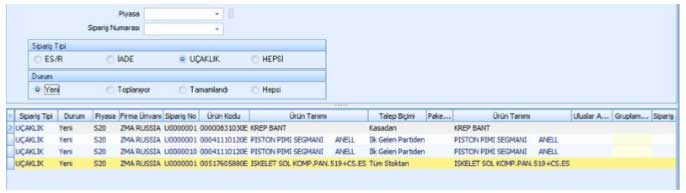
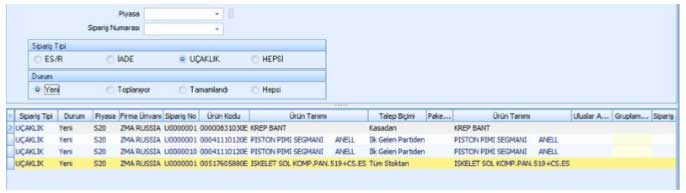
- It is an application prepared to prevent the materials that need to be shipped by plane for any reason from being sent by ship and to guarantee that they are shipped by plane.
- Aircraft shipment requests can be made for stocks in three different statuses: from the first incoming batch, from free stocks and from stocks with crates.
- The system checks the part number, airfreight quantity and the shipping method selected from any of the three statuses mentioned above.
- For example; if it is selected from the first arriving batch, it generates a warning message informing the material acceptance operators of the first arrival of the subject material that the material is aircraft and allows the subject part to be read only to the crates selected as aircraft by placing a special block on the stock tracking number (pallet number) of the material taken into stock. The case created as an airplane can only be read to the shipments opened as airplane.
- With this application, thanks to the control made by the system during the part entry, packaging and shipment, it prevents the operator from making mistakes and ensures that the part is shipped on time and in the desired status.
Depo- X / CM – Material Collection System
- It is a valid practice in markets working with Lot Order.
- The lot order is designed for the picking of small parts such as screws, washers, etc. that do not have a specific in-case plan, which is called Minüteri.
- Among the lots for which an order has been initiated through the system, the lots whose priorities are determined by the operation supervisor are selected. The system creates a shelf-based picking order for all of the Minüteri parts of the selected lots.
- Shelf responsibility areas have been determined for the personnel in charge of collecting materials. These areas are defined in the system. At the beginning of the shift, the personnel start collecting the parts for which a collection order has been created in their area of responsibility by following them on the hand terminal. The system provides flexibility to the personnel who are collecting, such as passing orders and changing lots. The personnel can print the labels of the collected parts by sending them to the IP printers located on the shelf with the hand terminal.
- On the printed labels, the number of the part, the quantity and the lot to which it belongs are indicated. The system also eliminates the problem of lot priority confusion as it does not allow the collected materials to be read in different lots. Personnel deliver the collected packaging to the area. The delivery process is done with the delivery-collection logic.
- Thanks to all these processes, it is possible to determine on which date and with which delivery note the material arrives, which personnel enters the delivery note into the system, which personnel gives quality approval, which personnel enters the stock, which personnel makes the stock entry, and which personnel is responsible for material acceptance.